ETAGE EPC
L' EPC se divise en 5 sous
systèmes le moteur Vulcain et son système d' activation tuyère, le réservoir
principal et la jupe avant.
La turbopompe H2 du moteur est fabriqué à le SEP à Vernon (France) et celle
O2 à Fiat Avio à Turin (Italie). la chambre de combustion par Damier Benz DASA
(depuis 2000 Astrium) à Ottobrunn en Allemagne et la tuyère par Volvo Aero
corporation à Trollhattan (Suède). Le moteur est assemblé à Vernon dans le
bâtiment de la Snecma-SEP. Les essais de mise à feu ont lieu sur deux banc
identiques le PF50 de la SEP à Vernon et le P5 de DLR à Lampoldshausen en
Allemagne.
Le réservoir principal est
en aluminium. il est composé de deux réservoirs à fond commun. L' enveloppe métallique est constituée de trois fonds et 7 viroles.
Le cycle de fabrication de l' EPC commence à DASA Dornier à Oberpfaffenhofen
(Allemagne) avec la fabrication des trois fonds, celui avant pour le réservoir
O2, celui arrière pour le réservoir H2 et le commun. Chaque fond comprend 8
secteurs et un anneau en Y qui sert d' interface entre le fond les autres
composants de l' EPC.
Les 7 viroles sont constituées de 3 panneaux préformés et soudés et sont
fabriqués par Cryospace dans l' usine des Mureaux à Paris. Les viroles et les
fonds sont ensuite soudées ensemble, timbrés (pour contrôler les fuites) et
équipés avant d' être remis à l' usine de l' Aerospatiale (depuis 2000 EADS)
sur le même site pour être assemblé.
La jupe avant est aussi en aluminium et composites à fibres. Elle abritent le
dispositif de poussée des EAP, les attaches EAP et le système de séparation.
Elle est fabriqué chez MAN Technologie à Augsbourg (Allemagne) puis livré aux
Mureaux pour intégration avec l' EPC.
Le bâti moteur est assemblé dans l' usine Spécial Products de Fokker à
Hoogeveen aux pays Bas avant expédition aux Mureaux.
L' unité d' activation de la tuyère est développée et fabriquée chez SABCA
près de Bruxelles (Belgique).
Tous les éléments de l' étage se retrouvent aux Mureaux pour être assemblés
et testés dans une installation spéciale. Le même dispositif est installé à
Kourou et entièrement compatible avec celui des Mureaux.
L' étage assemblé est mis
dans un container remorque et amené par péniche sur la Seine jusqu' au
Havre.
INSTALLATIONS D'ESSAIS ET D'ASSEMBLAGE MOTEUR
VULCAIN ET EPS
Les installations sont situées chez
Microtecnica en Italie à l'installation principale de Turin (assemblage
et essais de vérification) et au centre d'essais de Luserne (essais de
performance) dans deux salles blanches classe 100 000 de 115 mètres carré
(Turin) et 135 mètres carré pour Ariane 5 (Luserne).
Elle réalise les essais de performance du
moteur Vulcain et des équipements de l'étage cryotechnique ainsi que les essais
de vérification pendant l'assemblage sur le module de régulation de pression,
les équipements et vannes électro-magnétiques et les vannes à clapets.
Systèmes principaux :
_ Banc d'essais pour fuites et fissures
pendant l'assemblage (clapets, vannes électro-magnétiques, équipements)
_ Banc d'essais pour fuites, débit, temps de réponse, cycle de commutation,
stabilité du débit du module de régulation de la pression
_ Banc d'essais d'étanchéité, fuites, débit, temps de réponse, cycle de
commutation des clapets, vannes électro-magnétiques et des équipements sous
différentes conditions de température
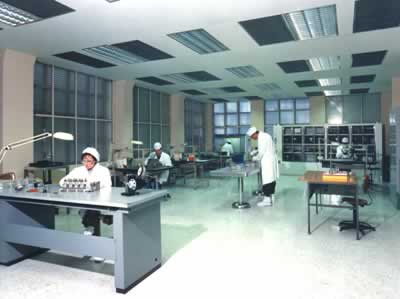
Active dans le secteur
spatial depuis 1973, la société Techspace Aero est spécialisée dans la
conception, définition, fabrication, montage et essais de réception
d'éléments du moteur Vulcain, de l'étage principal cryotechnique et de l’étage
à ergol stockable.
Elle assure à Herstal en
Belgique la fabrication, assemblage, essais et réception des vannes d'injection
chambre, vannes de purge, vannes gaz chaud du moteur Vulcain, vanne de
remplissage hélium et soupape de sécurité de l'enveloppe interne du
sous-système hélium de l'étage principal cryotechnique et vanne de sécurité
du réservoir ergol stockable du deuxième étage dans des salles blanches en
classe 100 et10 000 pour les composants cryogéniques et 300 000 pour le montage
et les essais des vannes.
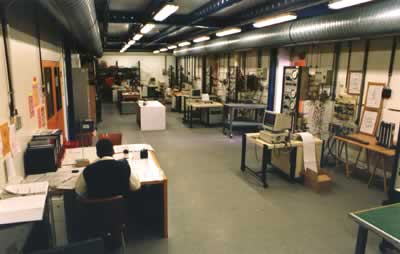
Le hall de montage du moteur
Vulcain est un bâtiment situé à Vernon en france. il est équipé d' un salle
blanche pour l'assemblage du moteur Vulcain, la préparation des matériels pour essais,
le démontage après essais pour expertises et remises en état.
Il possède une salle
blanche de 1220 mètres carré, un magasin
de 700 mètres carré, une logistique de 450 mètres carré, un sous-sol technique
de 1440 mètres carré et des bureaux de 1150
mètres carré.
Le bâtiment est aussi
équipé de pont roulant, de cinq centrales d' air et d' un réseaux de
gaz.
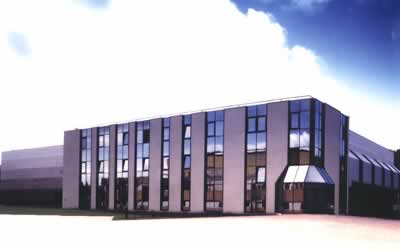
CONTENEURS DE TRANSPORT DU MOTEUR VULCAIN
4 conteneurs permettant le stockage et le transport des moteurs
Vulcain pour la mise au banc d'essais moteur (France ou Allemagne) et l'intégration lanceur (France ou Guyane).
Ils mesure 4 m de long sur 3 de large.
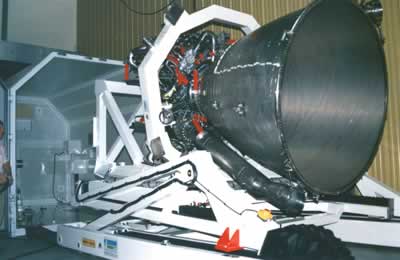
LE BATIMENT DE FABRICATION DES RESERVOIRS CYROTECHNIQUES
Crée par le G.I.E. CRYOSPACE (AIR LIQUIDE, EADS-LV),
il assure le développement et la fabrication du réservoir intégré équipé de
l'étage principal cryotechnique. L'usine permet l'assemblage par soudage des panneaux viroles et fonds de
réservoirs puis le timbrage, la pose de l'isolation et des équipements du
réservoir.
Accolé au bâtiment d' assemblage, il occupe
une surface au sol de 15 000 m2 avec une hauteur de 12 m et comprend:
_ Les bancs de soudage virole et réservoir
_ Le puits de timbrage
_ L' installation de
dégraissage
_ L' atelier peinture
_ L' atelier isolation
_ L' atelier de fabrication et pose des équipements
FABRICATION DE L' ETAGE EPC
Tout commence par la fabrication des
panneaux des viroles, et des secteurs de fond des réservoirs. Chaque
EPC est constitué de sept viroles et de trois fonds. Chaque virole
comprend trois panneaux.
Pour mettre en forme les grandes tôles usinées à plat de l’Etage
Principal Cryogénique d’Ariane 5, Aerospatiale aux Mureaux a
investit dans un tout nouvel atelier.
Ultra-propre, cet atelier permet la production en série des panneaux
constituant les viroles. Outil dernier cri, il garantit une production
en petite série tout en respectant les coûts et les délais. La réalisation
des panneaux pour le vol 505 a qualifié la gamme d’usinage et de préparation
du réservoir
Tout d’abord, les tôles brutes de
laminage, en alliage d’aluminium 2219 de trois mètres sur six mètres,
sont usinées dans le sens de l’épaisseur sur une fraiseuse double tête
d’usinage équipée d’électrobroches grande vitesse de 60 kW.
Lors de cet usinage, des bossages et des sur-épaisseurs bien déterminées
sont exécutées sur une face «dans la masse». Elles serviront à
accrocher les différents accessoires sur la structure du réservoir.
D’autre part, des «trottoirs» en périphérie des tôles serviront
à leur manutention, puis de sur-épaisseurs de soudage lors de
l’assemblage des viroles. L’autre face de la tôle reste entièrement
lisse. La section de chaque panneau varie entre 1,7 et 20 mm. La sur-épaisseur
initiale du brut est de 3 mm supplémentaire sur chaque face.
Les panneaux sont tenus sur la fraiseuse par une table à dépression de
4 x 16 m Un contrôle automatique d’épaisseur finie est associé à
ce poste.
Parallèlement aux quartiers de viroles usinés à plat, les brides
servant à relier les viroles entre-elles sont aussi «taillées dans la
masse». Monolithes, ces brides sont usinées par tournage vertical. Les
ébauches d’origine pèsent 300 kg. Les pièces finies n’excèdent
pas 50 kg avec une tolérance de plus ou moins un dixième de millimètre
sur leurs 5400 mm du diamètre.
Après un dégraissage soigné, les panneaux plans sont fournis à
l’atelier de formage. Installée dans une fosse, une machine spéciale
de cintrage utilise comme élément principal une presse NFM (Neyrpic
Framatome Mécanique). Son originalité réside dans ses poinçons
universels modulables, pilotés électoniquement.
L’automatisation de la séquence de cintrage est assurée par un
calculateur couplé en amont et spécialement programmé pour chaque
type de panneau. Une commande numérique pilote la presse, la table
amont et le réceptacle des panneaux.
Le cintrage à froid est obtenu par croquage sur chaque panneau, c’est
à dire par flexions successives d’amplitude et de pas biens définis.
Chaque tôle subit plus de 250 plis répartis sur toute sa longueur.
Pour chaque pli, le réglage de la ligne des poinçons est déterminé
par un ordinateur qui modifie automatiquement la configuration et la
cote des poinçons. Cette unité autorise la mise en forme des panneaux
de six mètres de long qui atteindront le diamètre de 5,4 m à la
fin de leur mise en forme. En prise directe avec le système
informatique, un contrôle de forme sur le bâti de référence est
effectué par 42 palpeurs montés sur un cercle mobile autorisant un
maillage précis.
Constituée de trois sous-ensembles, l’encombrement de cette presse
est globalement de 16 m sur 4 m. Le niveau inférieur de la fosse
qui la reçoit est situé à trois mètres en contrebas du plancher de
l’atelier. Son poids dépasse 40 tonnes.
Une fois mis en forme, les panneaux latéraux
et les fonds de réservoirs (cf : Une Technologie innovante : le
formage revenu paru dans le même numéro) sont transférés avec précaution
vers le GIE Cryospace.
Installé sur le site des Mureaux dans un bâtiment moderne ultra-propre
de 15 000 m2 mitoyen du hall d’intégration de tout l’étage
principal cryogénique, la filiale d’Air Liquide et d’Aérospatiale
dispose des moyens de soudage et de mise à l’épreuve des
gigantesques et fragiles réservoirs.
Une fois l’étage totalement intégré avec son moteur Vulcain, le
tout est chargé dans un container spécial qui, via la Seine toute
proche et le port du Havre, sera véhiculé jusqu’au pas de tir de
Kourou (Guyane).
Mais auparavant, Cryospace réceptionne les tôles cintrées, les
ausculte sous toutes les coutures par courants de Foucault avant de les
souder sur leurs brides. C’est ainsi que naissent les viroles complètes.
Délicats, manutention et soudage font appel à des vireurs basculeurs
puis à des portiques spéciaux.
Plus gigantesque encore, le banc de soudage final (OES) associant un
outillage de grandes dimensions sert à assembler les viroles
entre-elles. Ce même banc d’assemblage est aussi requis pour souder
des trois hémisphères délimitant les réservoirs hydrogène et oxygène.
Enfin complet, le réservoir endure une série d’examens et de contrôles
non destructifs (CND), puis est introduit dans un tunnel de traitement
de surface.
Dernière épreuve, il est introduit dans une fosse spécialement aménagée
pour y subir son épreuve de timbrage afin de contrôler la totale étanchéité
des deux cuves. Enfin, dans une salle spéciale, l’EPC reçoit une
partie de sa tuyauterie externe et son isolation thermique de 21 mm d’épaisseur
constituée d’un feutre Dacron et d’un Liner aluminisé double face.
Ainsi équipé, il rejoint enfin le bâtiment d’assemblage de l’étage
pour y recevoir ses équipements définitifs et surtout le fameux moteur
Vulcain, sa principale raison d’être...
Pressedition, janvier 1998 |
Le bâtiment de timbrage est haut de 41 m, il
permet l' érection du réservoir EPC et sa mise en place dans une fosse souterraine
de 50 m avec couvercle en béton destiné à vérifier les
éventuelles fuites du réservoir.
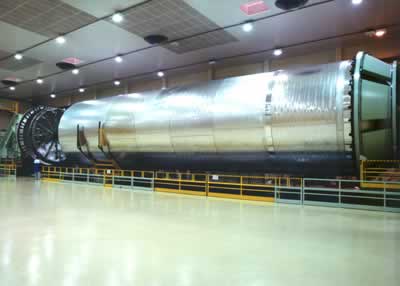
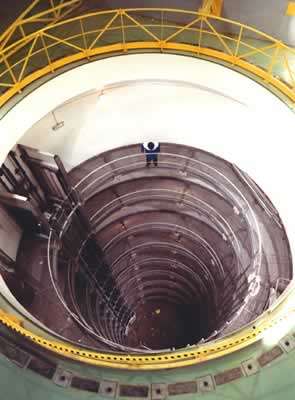
|